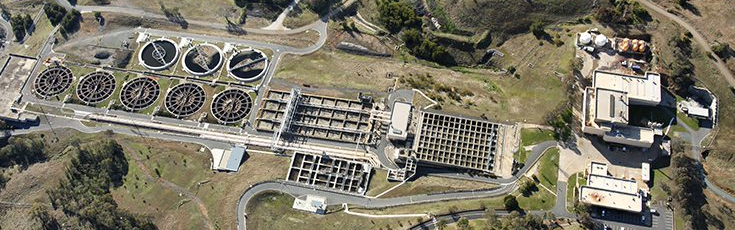
Lower Molonglo Water Quality Control Centre renewal: Bioreactors – secondary treatment process and Biosolids management
Our wastewater treatment plant has served Canberra’s needs for decades, but some of our assets are aging and elements of the treatment process are nearing capacity.
We have a responsibility to protect our environment and continue providing high-quality wastewater services to our community. To do this we need to upgrade, or replace, elements of our treatment process.
Our plans include two significant projects for our primary wastewater treatment plant, Lower Molonglo Water Quality Control Centre (LMWQCC). The first project is focused on our bioreactors and the other targets biosolids.
Click to enlarge
Bioreactors – secondary treatment process
Our current process
Microorganisms are a critical part of our wastewater treatment process. They convert the nitrogen found within our wastewater into nitrogen gas, minimising the impact on our river ecosystem. Something so vital to our treatment process, and the environment, needs dedicated infrastructure.
An opportunity to modernise
Our secondary treatment process is approaching capacity as Canberra’s population nears the half-million mark. New technologies present an opportunity to enhance performance on a range of measures, whilst also increasing capacity. Our team has investigated different options for upgrading the secondary treatment process in a staged approach to ensure we can service our community through the next 50 years.
How was the solution selected?
Icon Water assessed nine options and identified the risks and benefits of each, from which a shortlist was created to undergo further investigation:
- Option 1: Convert our existing bioreactors into a membrane bioreactor
A membrane bioreactor combines membrane filtration with a biological treatment process. - Option 2: Duplicate the existing process (with updated technology)
For this option, we would construct additional process trains but integrate similar but newer technology. - Option 3: Aerobic Granular Sludge (Nereda ®)
This trademarked process treats wastewater by creating compact sludge granules. - Option 4: Integrated Fixed Film Activated Sludge (IFAS)
The IFAS system consists of tanks filled with small pieces of plastic that create a habitat for microorganisms to attach and grow.
Options assessment:
These options went through a robust multi-criteria analysis to make sure we chose the best solution that factored in cost, the needs of our growing community, our environment and ensured our ability to treat wastewater to a high standard.
After rigorous assessment of suitable technologies, it was determined that our new biological treatment should be upgraded to membrane bioreactors, as Stage 1 of the project. Stage 2 will involve converting the existing bioreactor to membrane technology.
The staging of the project will allow for the infrastructure to be installed over time to spread out the cost and ensures it is right sized for the growing population.
Membrane technology stood out as the best option when assessed against the following criteria:
- Treatment process reliability, operability & maintainability
- Environmental impacts
- Community impacts
- Constructability and flexibility to adapt to future challenges
- Value for money for Icon Water’s customers (to find out how we fund these projects, see our factsheet on infrastructure funding).
- Ability to fit into the existing, space limited, site
How long will it take?
We are hoping to commence construction between 2025-28.
We will be engaging with the community as we progress this important project.
Project timeline
Click to enlarge
Biosolids treatment
Our current process
Canberra’s wastewater is separated into liquid and solids as part of the wastewater treatment process. These organic solids are known as biosolids.
Biosolids are placed within one of two furnaces, where the intense heat destroys pathogens and contaminants. This creates a product we call Agri-Ash, which retains elements of lime and phosphorus. Agri-Ash is a beneficial soil enhancer used on farmland. On average, we collect Agri-Ash three days per week for distribution to regional farmers.
An opportunity to improve
Both furnaces are approaching the end of their service life and maintenance is becoming increasingly expensive.
Our plan is to replace the old furnaces with an environmentally sustainable, and energy efficient technology to service our growing community over the next 50 years. We have consulted with experts, and industry partners, from across the globe to identify a shortlist of viable treatment alternatives.
How was the solution selected?
After carefully assessing 17 options, five were shortlisted. These shortlisted options would provide a reliable service that continues to protect human health and the environment. They would also help maximise resource recovery by producing energy or providing us with a product that can be re-used (like Agri-Ash).
Our options:
Of the 17 options we carefully assessed, five have been shortlisted:
- Option 1: Fluidised Bed Combustion (FBC)
This option is similar to our existing furnaces (by using intense heat) but is much more efficient and reliable. FBC produces electricity to offset our plant’s onsite use. It also creates an ash like the Agri-Ash we are already producing - Option 2: Anaerobic Digestion (AD)
This option processes the solids from wastewater using anaerobic biological processes. The biosolids produced by this process can be used on farmland. The methane produced can either be converted into electricity or used to dry biosolids. - Option 3: AD plus external biodegradable waste streams
This process is like Option 2, but it is amplified by extra waste streams from local industry. This helps others by taking their waste and creates more electricity from methane. - Option 4: AD plus off-site composting
This process is the same as Option 2, except it includes processing waste off site at a third-party composting facility. This composted product can be used on gardens or farmland. - Option 5: Gasification
This option is like Option 1, but combustion occurs in a low oxygen environment. The product from this process is a biochar which is more beneficial to agriculture than Agri-Ash because of its higher organic content. This process produces electricity to offset our plant’s onsite use.
Options assessment:
These options went through a robust multi-criteria analysis to make sure we chose the best solution that considered cost, the needs of our community, our environment and factored in circular economy opportunities.
After rigorous assessment of suitable options, high-tech heat treatment, known as Gasification, has been identified as the biosolids treatment solution that will provide the greatest community and environmental outcomes in terms of energy efficiency, enhanced resource recovery opportunities and ability to provide treatment of micro plastics and contaminants of emerging concern. The technology is auto thermal, meaning it needs an initial point of combustion for start-up, and then uses the biosolids as the ongoing fuel source to run. The initial combustion source is flexible, meaning that as the ACT transitions away from use of natural gas, we will not be bound to this energy source.
Gasification was the best performing technology out of all shortlisted options in terms of the following criteria:
- Emissions and climate change mitigation
- Energy recovery
- Truck movements
- Value for money for Icon Water’s customers (to find out how we fund these projects, see our factsheet on infrastructure funding).
- Circular economy benefits
- Flexibility to adapt to future challenges.
How long will it take?
We are hoping to commence construction between 2025-28.
We will be engaging with the community as we progress this important project.
Project timeline